Difference Between a Servo Motor and a Stepper Motor?
Difference Between a Servo Motor and a Stepper Motor?
Servo motors and stepper motors are both commonly used in precision control applications, but they have different characteristics and are suited to different types of tasks. Here’s a detailed comparison between the two:
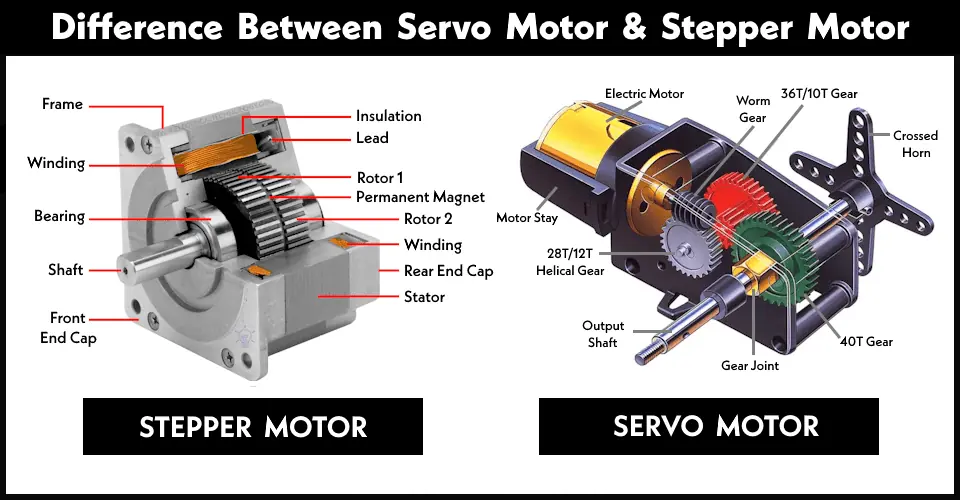
Servo Motor
- Operation:
- Utilizes a closed-loop system with feedback to control position, speed, and torque.
- Incorporates a feedback mechanism (typically an encoder) to monitor the actual position and adjust accordingly.
- Control:
- Continuous rotation with precise control over speed, position, and torque.
- Can reach and maintain specific positions accurately, even under varying loads.
- Torque:
- Provides high torque at high speeds.
- Capable of maintaining torque over a wide range of speeds, making it suitable for dynamic and high-performance applications.
- Complexity:
- Requires a more complex control system due to the need for feedback and error correction.
- Often involves a combination of a motor, controller, and feedback device (encoder or resolver).
- Applications:
- Ideal for applications requiring precise motion control, such as robotics, CNC machinery, and automated manufacturing.
- Used in systems where high torque and speed control are crucial.
Stepper Motor
- Operation:
- Utilizes an open-loop system without feedback for control.
- Moves in discrete steps, with each step corresponding to a fixed angle of rotation.
- Control:
- Provides precise control over position through incremental steps.
- Typically controlled by sending a sequence of pulses to the motor driver, with each pulse corresponding to one step.
- Torque:
- Provides high torque at low speeds.
- Torque decreases as speed increases, making it less suitable for high-speed applications.
- Complexity:
- Simpler control system compared to servo motors, as it does not require feedback mechanisms.
- Easier to set up and use, often with straightforward drivers and controllers.
- Applications:
- Suitable for applications requiring precise positioning at low speeds, such as 3D printers, scanners, and plotters.
- Commonly used in situations where holding torque is important, like in positioning systems and small-scale automation.
Key Differences
- Control System: Servo motors use a closed-loop system with feedback, while stepper motors use an open-loop system without feedback.
- Precision and Accuracy: Servo motors offer higher precision and accuracy due to their feedback mechanisms, whereas stepper motors provide good precision but are limited by step size and lack of feedback.
- Speed and Torque: Servo motors maintain high torque at high speeds and are better suited for dynamic applications, while stepper motors provide high torque at low speeds and are ideal for static or low-speed applications.
- Complexity and Cost: Servo motors are generally more complex and expensive due to the need for controllers and feedback devices, while stepper motors are simpler and more cost-effective.
In summary, servo motors are best for applications that require high precision, speed, and dynamic performance, while stepper motors are suitable for simpler, lower-speed applications where cost and ease of use are important.